ในยุคที่การแข่งขันในอุตสาหกรรมการผลิตเพิ่มสูงขึ้นและเทคโนโลยีเติบโตอย่างก้าวกระโดดในลักษณะเอ็กซ์โพเนนเชียล (Exponential Growth) ในปัจจุบัน ระบบ ERP/MRP ไม่เพียงช่วยเพิ่มประสิทธิภาพการผลิต แต่ยังช่วยให้องค์กรตอบสนองต่อการเปลี่ยนแปลงในตลาดได้อย่างรวดเร็วและยืดหยุ่น
โรงงานที่เลือกใช้ระบบ ERP/MRP ที่ถูกต้องจึงไม่เพียงอยู่รอดในยุคแห่งการแข่งขันนี้ แต่ยังสามารถก้าวขึ้นเป็นผู้นำในอุตสาหกรรมได้อย่างยั่งยืน
ERP (Enterprise Resource Planning) คือ ระบบซอฟต์แวร์ที่รวมข้อมูลและกระบวนการหลักขององค์กร เช่น การบัญชี การจัดซื้อ การขาย การผลิต
และการบริหารคลังสินค้า เข้าไว้ในแพลตฟอร์มเดียวกัน เพื่อให้ข้อมูลเป็นหนึ่งเดียว ลดความซ้ำซ้อน และช่วยให้องค์กรบริหารงานได้มีประสิทธิภาพและเห็นภาพรวมชัดเจนขึ้น
ซอฟต์แวร์ ERP สำหรับโรงงานอุตสาหกรรมมีความแตกต่างอย่างชัดเจนจากธุรกิจประเภทซื้อมา-ขายไป (Trading) หรือธุรกิจทั่วไป
ทั้งนี้ เนื่องจากโครงสร้างและกระบวนการผลิตในโรงงานอุตสาหกรรมมีความซับซ้อนกว่า
ดังนั้นการเลือกใช้ซอฟต์แวร์ ERP/MRP จากผู้ให้บริการรายใดก็ตามควรให้ความสำคัญกับโมดูลที่เป็นหัวใจหลักของระบบเสียก่อน
ระบบ ERP สำหรับโรงงานอุตสาหกรรมจำเป็นต้องมีโมดูลการวางแผนการผลิตและการคำนวณความต้องการวัสดุ (MPS/MRP System) เป็นแกนหลัก
หากโมดูล MRP ของซอฟต์แวร์ที่เลือกใช้ไม่สามารถคำนวณได้อย่างถูกต้อง
** ระบบ ERP ที่ได้มาก็จะเป็นเพียงโปรแกรมบัญชีที่ไม่สามารถตอบโจทย์ด้านการผลิตได้อย่างแท้จริง **
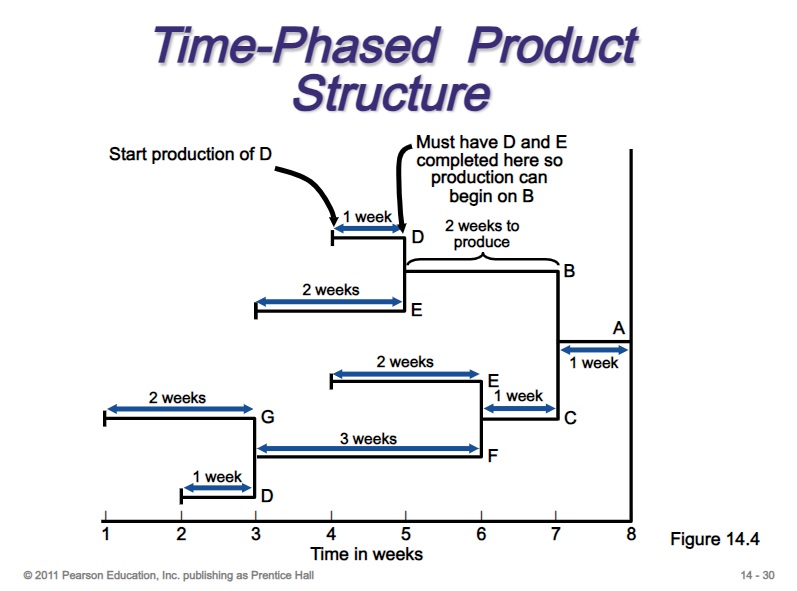
MRP LOGIC
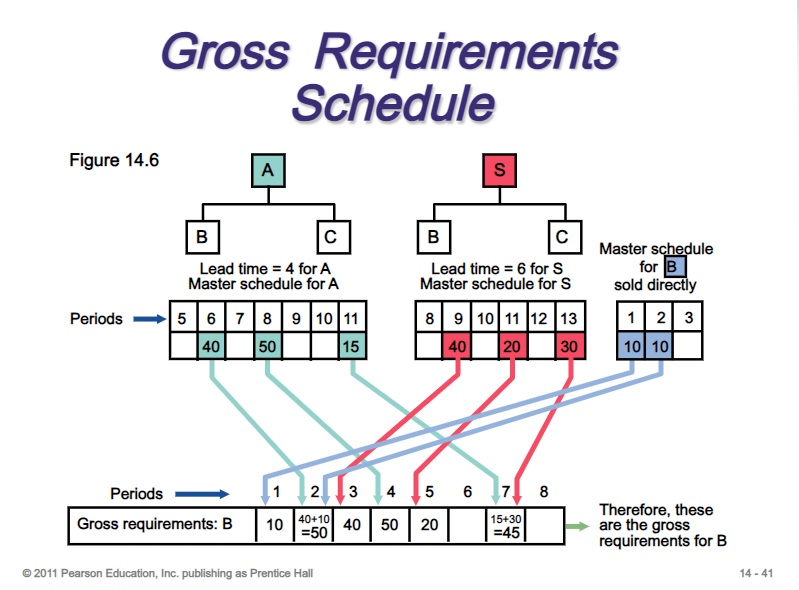
MRP LOGIC
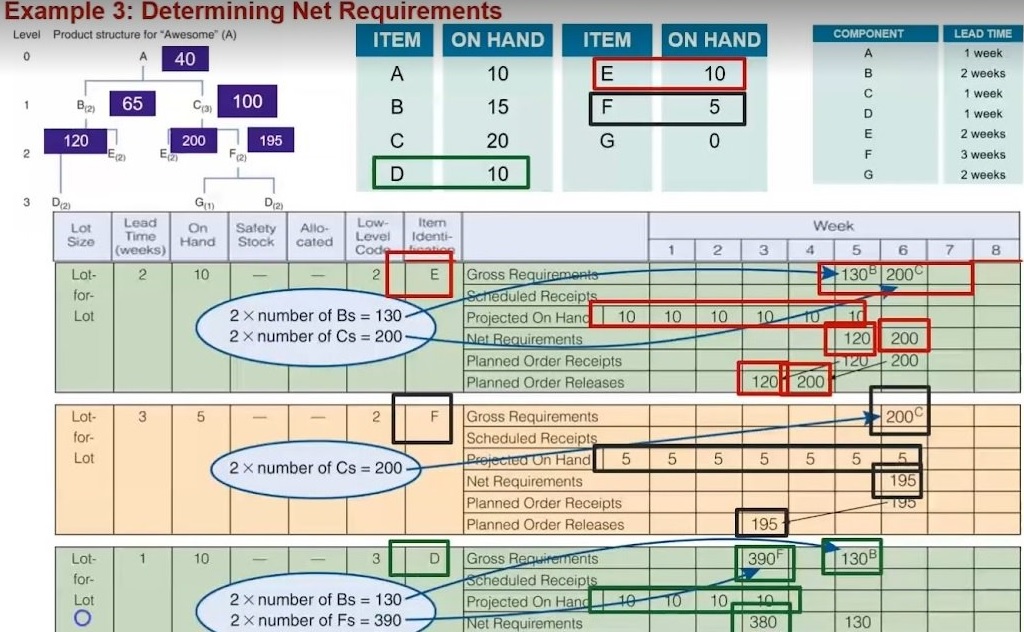
ตาราง MRP ตามทฤษฎี MRP
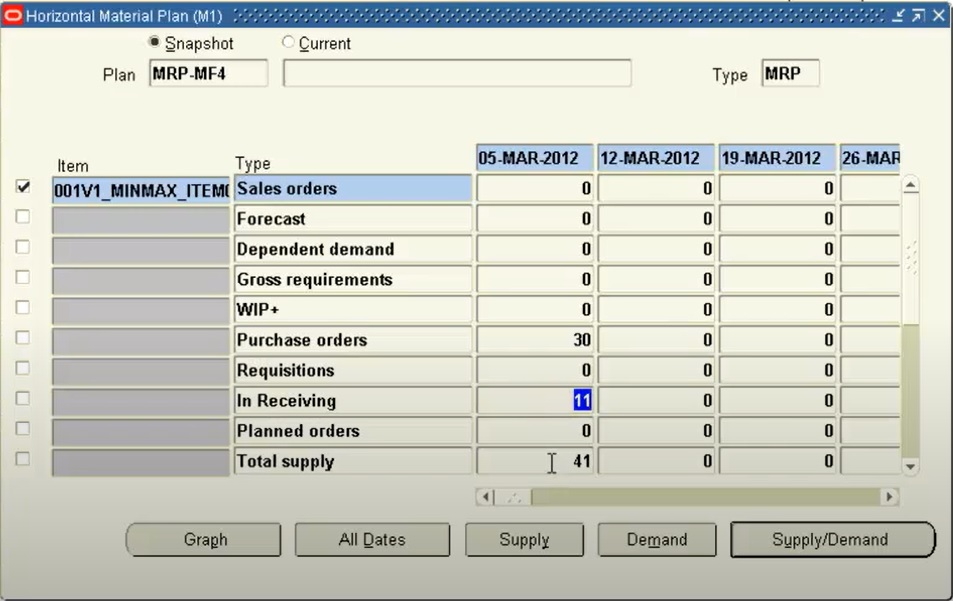
MRP TABLE OF ORACLE
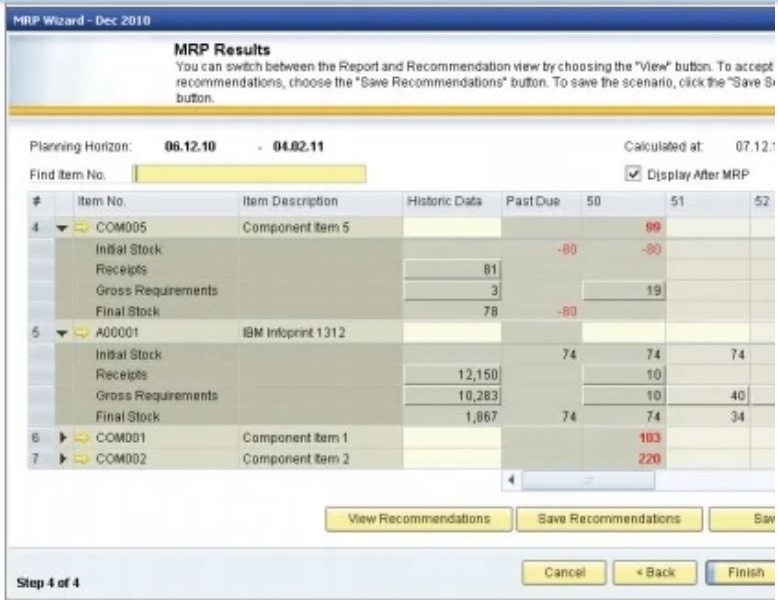
MRP TABLE OF SAP
MRP: ระบบวางแผนการผลิตที่โรงงานอุตสาหกรรมขาดไม่ได้ ในยุคดิจิทัล และ AI
(1) MRP (Material Requirements Planning) หรือระบบการวางแผนการผลิตและคำนวณความต้องการวัสดุ เป็นแกนสำคัญของอุตสาหกรรมการผลิต
การคำนวณ MRP จะต้องอ้างอิงพารามิเตอร์ที่ถูกต้องและคำนวณในรูปแบบตาราง MRP เท่านั้น โดยพารามิเตอร์หลักประกอบด้วย:
(2) องค์ประกอบและการคำนวณ MRP
2.1 Gross Requirement: ความต้องการวัสดุรวมในแต่ละช่วงเวลา
2.2 Scheduled Receipts: ปริมาณวัสดุที่มีกำหนดรับเข้าคลังในอนาคต
2.3 On-Hand Quantity: ปริมาณสินค้าหรือวัสดุคงเหลือในคลังปัจจุบัน
2.4 Net Requirement: ความต้องการสุทธิหลังหักปริมาณคงเหลือและวัสดุที่จะได้รับ
2.5 Planned Order Receipt: ปริมาณที่ต้องมีเพื่อรองรับการผลิตหรือการสั่งซื้อให้ตรงตามเวลาที่กำหนด
2.6 Planned Order Release: แผนการปล่อยคำสั่งผลิตหรือคำสั่งซื้อ โดยพิจารณา Lead Time
การคำนวณ MRP จะดำเนินการด้วยพารามิเตอร์ทั้ง 6 ตัวนี้ พร้อมกับช่วงเวลาที่แบ่งเป็นสัปดาห์ (Time-Phased)
การคำนวณ MRP ต้องเริ่มจากการระเบิดโครงสร้างผลิตภัณฑ์ (BOM) ของสินค้าสำเร็จรูปตามวันที่กำหนดส่งมอบ จากนั้นไล่ระดับลงสู่วัสดุแต่ละชนิดในทุกช่วงเวลาที่ต้องการ รวมถึงงานระหว่างผลิต (WIP) และวัตถุดิบและใช้ทั้ง 6 พารามิเตอร์อย่างต่อเนื่อง กระบวนการนี้มีความซับซ้อนสูง
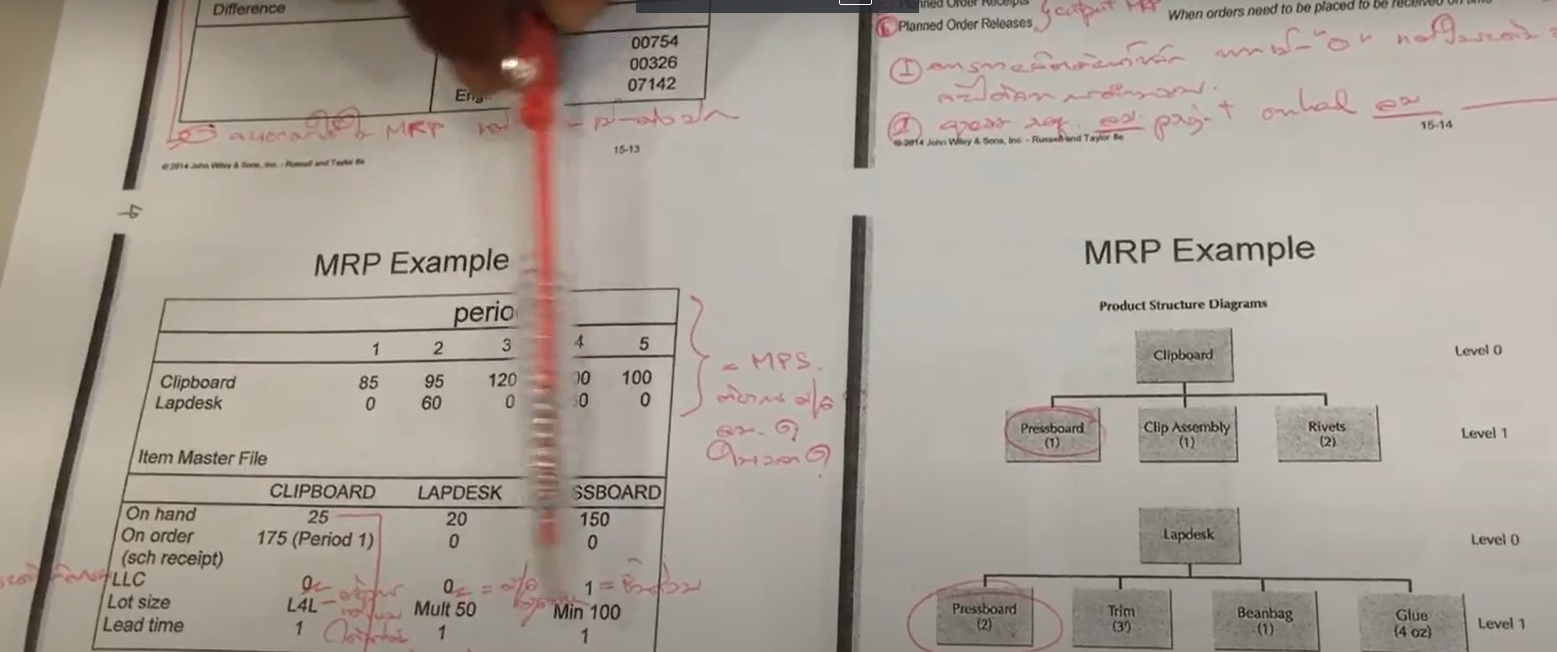
*
*** การคำนวณ MRP ***
https://www.youtube.com/watch?v=qbm_mfqdu58&t=90s
****ดังนั้นการคำนวณ MRP ที่ถูกต้องจึงไม่ใช่การนำยอดขาย (Sales Order) หรือการพยากรณ์ (Forecast) มาหักลบกับสินค้าคงคลัง,สินค้าค้างส่ง, Minimum Stock, BOM หรือคิดวิธีลัดอื่น ๆ เพราะวิธีดังกล่าวไม่ใช่ MRP ที่แท้จริง ****
(3) ผลกระทบจากการใช้ซอฟต์แวร์ MRP ที่คำนวณไม่ถูกต้อง
หากการคำนวณ MRP ไม่ถูกต้อง จะส่งผลต่อการวางแผนการผลิตทุกระดับ ตั้งแต่งานประกอบ (Assembly Part) งานระหว่างผลิต (Work-In-Process)
จนถึงงานผลิตสินค้าสำเร็จรูป (F/G) รวมถึงการจัดซื้อวัสดุจากซัพพลายเออร์ที่ผิดพลาดทั้งในปริมาณ รหัสวัสดุ และระยะเวลา ส่งผลกระทบในวงกว้างต่อประสิทธิภาพการดำเนินงานของโรงงาน
ดังนั้น การเลือกใช้ซอฟต์แวร์ ERP/MRP ที่คำนวณ MRP ได้อย่างถูกต้องจึงมีความสำคัญอย่างยิ่ง
ในปัจจุบัน มีซอฟต์แวร์มากมายที่อ้างว่าเป็น ERP และมีระบบ MRP แต่ไม่ใช่ทุกระบบที่เป็น ERP/MRP สำหรับโรงงานอย่างแท้จริง
ดังนั้นโรงงานที่กำลังเลือก ERP/MRP Software มาใช้จึงควรให้ความสำคัญกับการสอบถามรายละเอียดของ MPS/MRP จากผู้จำหน่ายทุกราย เพื่อหลีกเลี่ยงการเลือกซอฟต์แวร์ผิดพลาด ซึ่งนอกจากทำให้สูญเสียงบประมาณลงทุนแล้ว ยังสูญเสียเวลา โอกาส และทรัพยากรอื่น ๆ อีกมาก
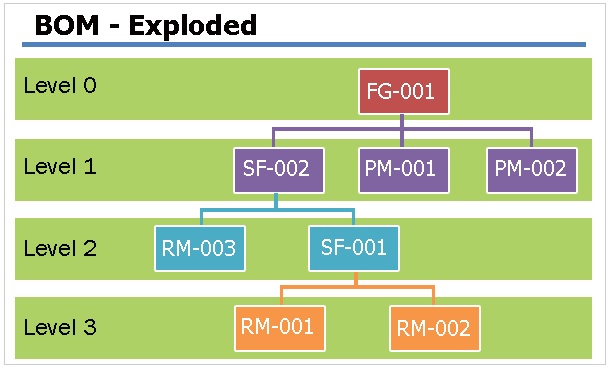
Bill of Materials ( BOM)
(4) แนวทางเร่งด่วนในการเลือกใช้ระบบ MRP ที่มีคุณภาพ
4.1 เนื่องจาก MRP คำนวณในรูปแบบตาราง MRP โดยใช้พารามิเตอร์ทั้ง 6 ตัวร่วมกับช่วงเวลาเป็นสัปดาห์ ผู้สนใจสามารถขอตัวอย่าง “ตาราง MRP” จากผู้จำหน่ายซอฟต์แวร์ได้
4.2 หากมีโอกาสได้รับการสาธิต (Demo) โปรแกรม ERP/MRP จากผู้จำหน่าย ควรให้ผู้จำหน่ายแสดงการคำนวณ MPS/MRP ตั้งแต่ขั้นตอนรับข้อมูล Sales Order หรือ Sales Forecast โดยเลือกสินค้าที่มี BOM ขั้นต่ำ 2-3 ระดับ (BOM Levels) และรันระบบด้วยรหัสสินค้า ซัก 2-3 ตัว ตั้งแต่ต้นจนจบ
หากการคำนวณ MRP ถูกต้อง
1. เมื่อดำเนินการจัดซื้อวัสดุตามคำแนะนำของ MRP (MRP Order Recommendation Plan) และนำวัสดุเข้าคลัง
2. MRP จะออกแผนการผลิตงานประกอบ (WIP) และสินค้าสำเร็จรูป (F/G) (MRP Production Recommendation Planning)
3. เปิดคำสั่งผลิต (Work Order) ตามคำแนะนำของ MRP
4. ปล่อย Work Order เดินสายการผลิตจนสินค้าสำเร็จพร้อมส่งออก
ในท้ายที่สุด วัสดุที่ MRP แนะนำให้สั่งซื้อ และงานประกอบที่เปิดผลิตจะถูกนำมาใช้จนหมด ( เป็นศูนย์ )
และแปรสภาพเป็นสินค้าสำเร็จในปริมาณเท่ากับ Sales Order ที่กำหนดไว้ หากเป็นเช่นนี้จึงพอจะมั่นใจได้ว่าระบบ MRP และ ERP
ของซอฟต์แวร์นั้นมีความน่าเชื่อถือและคำนวณได้อย่างถูกต้อง
ในโลกความเป็นจริง เราจะใช้โมดูลนี้ในการคำนวณแผนการปฏิบัติงานทุกวันในทุกแผนก และแบ่งปันแผนการแก่ทุกฝ่าย ทั้งคลังสินค้า (Warehouse), จัดซื้อ, ผลิต และอื่น ๆ เพื่อทำงานสอดประสานกันทั้งองค์กร การบริหารพื้นที่คลังสินค้าก็จะมีประสิทธิภาพยิ่งขึ้น วัสดุที่ยังไม่จำเป็นต้องใช้ในระยะเวลาอันใกล้ไม่จำเป็นต้องนำเข้าคลัง ผลลัพธ์สุดท้ายคือการลดต้นทุนโดยรวมและเพิ่มประสิทธิภาพในการดำเนินงานของทั้งองค์กร
ERP FACTORY SOFT CO.,LTD.
https://www.erpfactorysoft.com/
https://erpfactorysoft-usa.com/
การคำนวณ MRP ที่ถูกต้อง: กุญแจสู่ความสำเร็จในระบบ ERP โรงงานอุตสาหกรรรม
โรงงานที่เลือกใช้ระบบ ERP/MRP ที่ถูกต้องจึงไม่เพียงอยู่รอดในยุคแห่งการแข่งขันนี้ แต่ยังสามารถก้าวขึ้นเป็นผู้นำในอุตสาหกรรมได้อย่างยั่งยืน
ERP (Enterprise Resource Planning) คือ ระบบซอฟต์แวร์ที่รวมข้อมูลและกระบวนการหลักขององค์กร เช่น การบัญชี การจัดซื้อ การขาย การผลิต
และการบริหารคลังสินค้า เข้าไว้ในแพลตฟอร์มเดียวกัน เพื่อให้ข้อมูลเป็นหนึ่งเดียว ลดความซ้ำซ้อน และช่วยให้องค์กรบริหารงานได้มีประสิทธิภาพและเห็นภาพรวมชัดเจนขึ้น
ซอฟต์แวร์ ERP สำหรับโรงงานอุตสาหกรรมมีความแตกต่างอย่างชัดเจนจากธุรกิจประเภทซื้อมา-ขายไป (Trading) หรือธุรกิจทั่วไป
ทั้งนี้ เนื่องจากโครงสร้างและกระบวนการผลิตในโรงงานอุตสาหกรรมมีความซับซ้อนกว่า
ดังนั้นการเลือกใช้ซอฟต์แวร์ ERP/MRP จากผู้ให้บริการรายใดก็ตามควรให้ความสำคัญกับโมดูลที่เป็นหัวใจหลักของระบบเสียก่อน
ระบบ ERP สำหรับโรงงานอุตสาหกรรมจำเป็นต้องมีโมดูลการวางแผนการผลิตและการคำนวณความต้องการวัสดุ (MPS/MRP System) เป็นแกนหลัก
หากโมดูล MRP ของซอฟต์แวร์ที่เลือกใช้ไม่สามารถคำนวณได้อย่างถูกต้อง
** ระบบ ERP ที่ได้มาก็จะเป็นเพียงโปรแกรมบัญชีที่ไม่สามารถตอบโจทย์ด้านการผลิตได้อย่างแท้จริง **
MRP LOGIC
MRP LOGIC
ตาราง MRP ตามทฤษฎี MRP
MRP TABLE OF ORACLE
MRP TABLE OF SAP
MRP: ระบบวางแผนการผลิตที่โรงงานอุตสาหกรรมขาดไม่ได้ ในยุคดิจิทัล และ AI
(1) MRP (Material Requirements Planning) หรือระบบการวางแผนการผลิตและคำนวณความต้องการวัสดุ เป็นแกนสำคัญของอุตสาหกรรมการผลิต
การคำนวณ MRP จะต้องอ้างอิงพารามิเตอร์ที่ถูกต้องและคำนวณในรูปแบบตาราง MRP เท่านั้น โดยพารามิเตอร์หลักประกอบด้วย:
(2) องค์ประกอบและการคำนวณ MRP
2.1 Gross Requirement: ความต้องการวัสดุรวมในแต่ละช่วงเวลา
2.2 Scheduled Receipts: ปริมาณวัสดุที่มีกำหนดรับเข้าคลังในอนาคต
2.3 On-Hand Quantity: ปริมาณสินค้าหรือวัสดุคงเหลือในคลังปัจจุบัน
2.4 Net Requirement: ความต้องการสุทธิหลังหักปริมาณคงเหลือและวัสดุที่จะได้รับ
2.5 Planned Order Receipt: ปริมาณที่ต้องมีเพื่อรองรับการผลิตหรือการสั่งซื้อให้ตรงตามเวลาที่กำหนด
2.6 Planned Order Release: แผนการปล่อยคำสั่งผลิตหรือคำสั่งซื้อ โดยพิจารณา Lead Time
การคำนวณ MRP จะดำเนินการด้วยพารามิเตอร์ทั้ง 6 ตัวนี้ พร้อมกับช่วงเวลาที่แบ่งเป็นสัปดาห์ (Time-Phased)
การคำนวณ MRP ต้องเริ่มจากการระเบิดโครงสร้างผลิตภัณฑ์ (BOM) ของสินค้าสำเร็จรูปตามวันที่กำหนดส่งมอบ จากนั้นไล่ระดับลงสู่วัสดุแต่ละชนิดในทุกช่วงเวลาที่ต้องการ รวมถึงงานระหว่างผลิต (WIP) และวัตถุดิบและใช้ทั้ง 6 พารามิเตอร์อย่างต่อเนื่อง กระบวนการนี้มีความซับซ้อนสูง
**** การคำนวณ MRP ***
https://www.youtube.com/watch?v=qbm_mfqdu58&t=90s
****ดังนั้นการคำนวณ MRP ที่ถูกต้องจึงไม่ใช่การนำยอดขาย (Sales Order) หรือการพยากรณ์ (Forecast) มาหักลบกับสินค้าคงคลัง,สินค้าค้างส่ง, Minimum Stock, BOM หรือคิดวิธีลัดอื่น ๆ เพราะวิธีดังกล่าวไม่ใช่ MRP ที่แท้จริง ****
(3) ผลกระทบจากการใช้ซอฟต์แวร์ MRP ที่คำนวณไม่ถูกต้อง
หากการคำนวณ MRP ไม่ถูกต้อง จะส่งผลต่อการวางแผนการผลิตทุกระดับ ตั้งแต่งานประกอบ (Assembly Part) งานระหว่างผลิต (Work-In-Process)
จนถึงงานผลิตสินค้าสำเร็จรูป (F/G) รวมถึงการจัดซื้อวัสดุจากซัพพลายเออร์ที่ผิดพลาดทั้งในปริมาณ รหัสวัสดุ และระยะเวลา ส่งผลกระทบในวงกว้างต่อประสิทธิภาพการดำเนินงานของโรงงาน
ดังนั้น การเลือกใช้ซอฟต์แวร์ ERP/MRP ที่คำนวณ MRP ได้อย่างถูกต้องจึงมีความสำคัญอย่างยิ่ง
ในปัจจุบัน มีซอฟต์แวร์มากมายที่อ้างว่าเป็น ERP และมีระบบ MRP แต่ไม่ใช่ทุกระบบที่เป็น ERP/MRP สำหรับโรงงานอย่างแท้จริง
ดังนั้นโรงงานที่กำลังเลือก ERP/MRP Software มาใช้จึงควรให้ความสำคัญกับการสอบถามรายละเอียดของ MPS/MRP จากผู้จำหน่ายทุกราย เพื่อหลีกเลี่ยงการเลือกซอฟต์แวร์ผิดพลาด ซึ่งนอกจากทำให้สูญเสียงบประมาณลงทุนแล้ว ยังสูญเสียเวลา โอกาส และทรัพยากรอื่น ๆ อีกมาก
Bill of Materials ( BOM)
(4) แนวทางเร่งด่วนในการเลือกใช้ระบบ MRP ที่มีคุณภาพ
4.1 เนื่องจาก MRP คำนวณในรูปแบบตาราง MRP โดยใช้พารามิเตอร์ทั้ง 6 ตัวร่วมกับช่วงเวลาเป็นสัปดาห์ ผู้สนใจสามารถขอตัวอย่าง “ตาราง MRP” จากผู้จำหน่ายซอฟต์แวร์ได้
4.2 หากมีโอกาสได้รับการสาธิต (Demo) โปรแกรม ERP/MRP จากผู้จำหน่าย ควรให้ผู้จำหน่ายแสดงการคำนวณ MPS/MRP ตั้งแต่ขั้นตอนรับข้อมูล Sales Order หรือ Sales Forecast โดยเลือกสินค้าที่มี BOM ขั้นต่ำ 2-3 ระดับ (BOM Levels) และรันระบบด้วยรหัสสินค้า ซัก 2-3 ตัว ตั้งแต่ต้นจนจบ
หากการคำนวณ MRP ถูกต้อง
1. เมื่อดำเนินการจัดซื้อวัสดุตามคำแนะนำของ MRP (MRP Order Recommendation Plan) และนำวัสดุเข้าคลัง
2. MRP จะออกแผนการผลิตงานประกอบ (WIP) และสินค้าสำเร็จรูป (F/G) (MRP Production Recommendation Planning)
3. เปิดคำสั่งผลิต (Work Order) ตามคำแนะนำของ MRP
4. ปล่อย Work Order เดินสายการผลิตจนสินค้าสำเร็จพร้อมส่งออก
ในท้ายที่สุด วัสดุที่ MRP แนะนำให้สั่งซื้อ และงานประกอบที่เปิดผลิตจะถูกนำมาใช้จนหมด ( เป็นศูนย์ )
และแปรสภาพเป็นสินค้าสำเร็จในปริมาณเท่ากับ Sales Order ที่กำหนดไว้ หากเป็นเช่นนี้จึงพอจะมั่นใจได้ว่าระบบ MRP และ ERP
ของซอฟต์แวร์นั้นมีความน่าเชื่อถือและคำนวณได้อย่างถูกต้อง
ในโลกความเป็นจริง เราจะใช้โมดูลนี้ในการคำนวณแผนการปฏิบัติงานทุกวันในทุกแผนก และแบ่งปันแผนการแก่ทุกฝ่าย ทั้งคลังสินค้า (Warehouse), จัดซื้อ, ผลิต และอื่น ๆ เพื่อทำงานสอดประสานกันทั้งองค์กร การบริหารพื้นที่คลังสินค้าก็จะมีประสิทธิภาพยิ่งขึ้น วัสดุที่ยังไม่จำเป็นต้องใช้ในระยะเวลาอันใกล้ไม่จำเป็นต้องนำเข้าคลัง ผลลัพธ์สุดท้ายคือการลดต้นทุนโดยรวมและเพิ่มประสิทธิภาพในการดำเนินงานของทั้งองค์กร
ERP FACTORY SOFT CO.,LTD.
https://www.erpfactorysoft.com/
https://erpfactorysoft-usa.com/